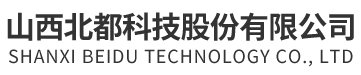
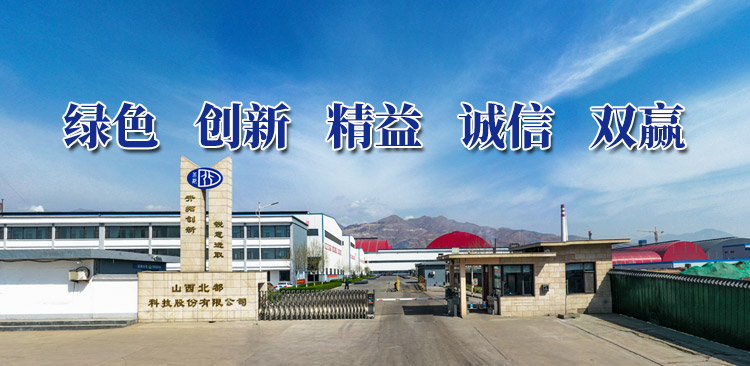

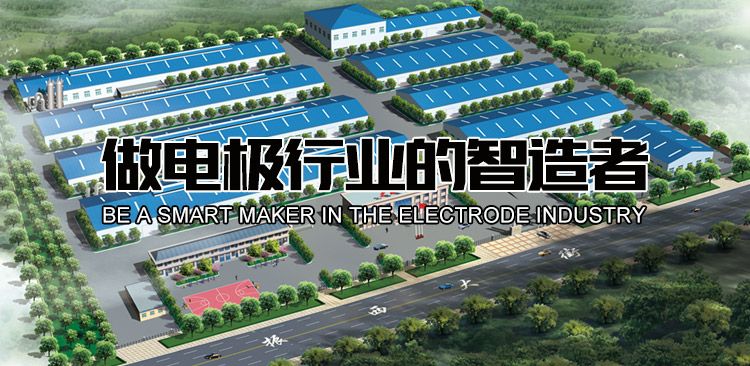
【“三高”論文推薦】姜周華:電弧爐煉鋼技術(shù)的發(fā)展趨勢
編輯:2023-10-30 16:07:46
電弧爐煉鋼技術(shù)的發(fā)展趨勢
姜周華1,2,姚聰林1,朱紅春1,潘濤1
(1. 東北大學(xué)冶金學(xué)院, 遼寧 沈陽 110819;2. 東北大學(xué)軋制技術(shù)及連軋自動化國家重點(diǎn)實(shí)驗(yàn)室, 遼寧 沈陽 110819)
摘要:電弧爐煉鋼在環(huán)保、投資以及效率方面優(yōu)勢明顯,為了重點(diǎn)推行該節(jié)能環(huán)保型煉鋼工藝流程,近年來電弧爐煉鋼技術(shù)得到快速發(fā)展。綜述了國內(nèi)外電弧爐*化冶煉技術(shù)、綠色化生產(chǎn)技術(shù)和智能化控制技術(shù)的發(fā)展現(xiàn)狀,其中綠色化和智能化是電弧爐煉鋼技術(shù)的未來發(fā)展趨勢。集操作、工藝、質(zhì)量、成本以及環(huán)保于一體,進(jìn)一步提升電弧爐煉鋼技術(shù)的綠色化和全流程監(jiān)測與控制的智能化,是推動整個鋼鐵行業(yè)向智能化和綠色化轉(zhuǎn)型升級的重要舉措。
關(guān)鍵詞:電弧爐煉鋼; 廢鋼預(yù)熱; *化; 綠色化; 智能化
電弧爐是一種利用電弧熱效應(yīng),將電能轉(zhuǎn)變?yōu)闊崮?,并通過輻射和電弧直接作用加熱并熔化金屬的設(shè)備;電弧爐煉鋼在環(huán)保、投資以及效率上占據(jù)諸多優(yōu)勢。在全球范圍內(nèi)電爐鋼產(chǎn)量占鋼總產(chǎn)量比例已從20世紀(jì)50年代初的7.3%提高到32%~35%。2018年全球電爐鋼平均占比為28.8%,其中美國為68%、歐盟為41.5%、日本為25%,而中國僅約為11.6%,明顯低于平均水平,較低的電爐鋼比例是造成鋼鐵工業(yè)能耗高、污染大的重要原因之一。目前,全球范圍內(nèi)95%以上電爐鋼產(chǎn)量是由電弧爐生產(chǎn)制備的,以電弧爐煉鋼為核心的短流程煉鋼已經(jīng)成為整個鋼鐵生產(chǎn)的重要流程之一?!白⒅匾詮U鋼為原料的短流程電爐煉鋼發(fā)展”是實(shí)現(xiàn)鋼鐵工業(yè)可持續(xù)發(fā)展的重大戰(zhàn)略決策之一。
縱觀發(fā)展歷程,電弧爐煉鋼圍繞著“節(jié)能降耗、提高生產(chǎn)率”的總體目標(biāo),研發(fā)了一系列相關(guān)技術(shù)。20世紀(jì)60-70年代,電弧爐煉鋼技術(shù)的發(fā)展以提升生產(chǎn)率為主導(dǎo),開發(fā)了超高功率電弧爐及相關(guān)技術(shù);80-90年代,強(qiáng)化用氧技術(shù)趨于成熟;為了進(jìn)一步節(jié)能降耗、縮短冶煉周期,廢氣的余熱利用逐步受到重視,并研發(fā)了一系列廢鋼預(yù)熱技術(shù),如料籃式、雙爐殼式、豎爐式以及水平連續(xù)加料式等。與此同時,環(huán)境保護(hù)意識的加強(qiáng)及人工智能技術(shù)的快速發(fā)展,對電弧爐煉鋼技術(shù)提出了新要求,指明了新發(fā)展方向。電弧爐煉鋼技術(shù)融合了各種現(xiàn)代裝備及其配套技術(shù)的綜合技術(shù),在*化冶煉基礎(chǔ)上,智能化及綠色化是電弧爐未來發(fā)展方向。本文通過綜述近年來電弧爐煉鋼技術(shù)發(fā)展現(xiàn)狀,探討了電弧爐煉鋼技術(shù)的未來發(fā)展方向。
1
電弧爐*化冶煉技術(shù)
電弧爐*化生產(chǎn)具備全局協(xié)同、連續(xù)化生產(chǎn)等特點(diǎn)。電弧爐冶煉工藝*化的目標(biāo)是減少通電時長、縮短冶煉周期以及*大限度降低冶煉電耗;具體措施主要包括提升功率、提高化學(xué)能輸入強(qiáng)度和減少非通電操作時間等。
1.1電弧爐爐容大型化
生產(chǎn)實(shí)踐證明,在技術(shù)經(jīng)濟(jì)指標(biāo)方面(如冶煉用電、電極單耗以及成本等),大型電弧爐的生產(chǎn)率及能源利用率均高于中小型電弧爐。目前,電弧爐正朝著爐容大型化方向發(fā)展。工業(yè)發(fā)達(dá)國家主流電弧爐容量為80~150 t,且已逐步增至150~200 t。如意大利達(dá)涅利公司(DANIELI)成功制造了全球*大爐容量為420 t的直流電弧爐,如圖1所示,該電弧爐設(shè)計(jì)生產(chǎn)率為360 t/h,具有*率、低運(yùn)行成本的特點(diǎn),能提升鋼廠生產(chǎn)效率和鋼的品質(zhì);已用于生產(chǎn)低碳鋼、超低碳鋼和高級脫氧*鋼,年產(chǎn)量為260萬t。
根據(jù)中國工業(yè)和信息化部等相關(guān)部門統(tǒng)計(jì),2015年中國電弧爐分噸位生產(chǎn)能力比例如圖2所示;國內(nèi)100 t及以上的大容量電弧爐產(chǎn)能占電弧爐煉鋼總產(chǎn)能的30.8%,占比*高;75 t及以上電弧爐產(chǎn)能占電弧爐煉鋼總產(chǎn)能的56.6%。此外,60 t以下的落后產(chǎn)能還有21.9%,這表明在環(huán)保限產(chǎn)和淘汰落后產(chǎn)能政策引導(dǎo)下,國內(nèi)鋼廠在通過產(chǎn)能置換提升電弧爐效率方面仍存在較大空間。
2018年國內(nèi)新增電弧爐中70~120 t公稱容積所占比例為80%。中國電弧爐正朝著裝備大型化和現(xiàn)代化快速發(fā)展,但與工業(yè)發(fā)達(dá)國家之間仍存在較大差距。
1.2超高功率供電技術(shù)
根據(jù)供電功率大小,電弧爐變壓器可分為普通功率(RP)、高功率(HP)和超高功率(UHP) 3類。從20世紀(jì)60年代至今,超高功率電弧爐煉鋼的理念主導(dǎo)了近60年電弧爐煉鋼生產(chǎn)技術(shù)的發(fā)展,其核心思想是*大限度地發(fā)揮主變壓器能力。大功率電弧爐變壓器是滿足電弧爐煉鋼*化、實(shí)現(xiàn)超高功率供電的基礎(chǔ)。制造商制造100 t電弧爐變壓器的主要參數(shù)及技術(shù)經(jīng)濟(jì)指標(biāo)見表1。
要實(shí)現(xiàn)超高功率供電,起協(xié)調(diào)電力波動和穩(wěn)定電弧作用的科學(xué)合理供電制度尤為重要。墨西哥泰納Tamsa鋼廠為優(yōu)化供電制度,在2016年和2017年期間開發(fā)并應(yīng)用了具備修改和優(yōu)化電弧爐供電制度功能的模型,該模型基于能量平衡(電能/化學(xué)能)、通電時間、電弧穩(wěn)定性、輻射指數(shù)等參數(shù)變化規(guī)律自動優(yōu)化供電曲線。Tamsa鋼廠利用此模型重新設(shè)計(jì)供電制度,在保持能耗水平基本不變的情況下,電弧爐產(chǎn)能提高了9.8%,生產(chǎn)率提升*明顯。
采用超高功率供電后的主要優(yōu)點(diǎn)有:縮短冶煉時間,提高生產(chǎn)效率;提高電熱效率,降低電耗;易與精煉、連鑄的生產(chǎn)節(jié)奏相匹配,從而實(shí)現(xiàn)*低耗生產(chǎn)。70 t電弧爐超高功率改造后,生產(chǎn)率由27提升至62 t/h,見表2。
1.3熔池?cái)嚢杓杉夹g(shù)
傳統(tǒng)電弧爐煉鋼熔池?cái)嚢鑿?qiáng)度較弱,爐內(nèi)物質(zhì)和能量傳遞較慢。采用超高功率供電、高強(qiáng)度化學(xué)能輸入等技術(shù),也未從根本上解決熔池?cái)嚢鑿?qiáng)度不 足和物質(zhì)能量傳遞速度慢等問題。為加快冶煉節(jié)奏,相繼研發(fā)了強(qiáng)化供氧和底吹攪拌等復(fù)合吹煉技術(shù),以及電磁攪拌技術(shù)等。新一代電弧爐熔池?cái)嚢杓夹g(shù)是集強(qiáng)化供氧、底吹攪拌及電磁攪拌等單元于一體,能滿足多元爐料條件下電弧爐冶煉的技術(shù)要求。
電弧爐煉鋼復(fù)合吹煉技術(shù)日趨成熟,已實(shí)現(xiàn)了工業(yè)推廣應(yīng)用,如中國的西寧特鋼、天津鋼管、新余特鋼、衡陽鋼管等企業(yè)均成功應(yīng)用了電弧爐煉鋼復(fù)合吹煉工藝,工業(yè)*良好,有效地降低了成本。中國部分電弧爐復(fù)合吹煉技術(shù)改造前后的工業(yè)*對比見表3。
與復(fù)合吹煉技術(shù)相比,電弧爐電磁攪拌技術(shù)普及面較窄,但其熔池?cái)嚢?更加優(yōu)異,工業(yè)應(yīng)用*反響良好。以ABB研發(fā)的電磁攪拌設(shè)備(ArcSave)為例,電磁攪拌技術(shù)有效提升了熔池中物質(zhì)和能量傳遞速率,更有利于廢鋼熔化,加速均勻鋼水成分及溫度,提高電弧爐產(chǎn)能。Steel Dynamics Inc(SDI)Roanode電弧爐ArcSave改造后相關(guān)指標(biāo)提升*,見表4。
1.4熱裝鐵水技術(shù)
由于電力資源的緊張和優(yōu)質(zhì)廢鋼資源的短缺,近年來,部分電弧爐煉鋼廠煉鋼過程中添加一定量鐵水,即鐵水熱裝的電弧爐煉鋼工藝,該工藝有效縮短電弧爐冶煉周期,同時幫助企業(yè)靈活應(yīng)對廢鋼市場價格波動,具備一定經(jīng)濟(jì)效益。
采用熱裝鐵水技術(shù)在電弧爐煉鋼過程應(yīng)用較普遍,如中國的中天鋼鐵公司和天津鋼鐵公司等,其中達(dá)涅利連續(xù)加料電弧爐(EAF ECS)為滿足添加鐵水的需要,對電弧爐進(jìn)行了特殊設(shè)計(jì)和改造。國內(nèi)某鋼廠的電弧爐熱裝鐵水后的電弧爐經(jīng)濟(jì)技術(shù)指標(biāo)見表5。實(shí)踐表明,現(xiàn)代電弧爐熱裝鐵水對于縮短冶煉周期、降低電耗等*非常顯著。
從長遠(yuǎn)來看,當(dāng)廢鋼冶煉成本與轉(zhuǎn)爐冶煉相當(dāng)或具備一定競爭力時,電弧爐冶煉生產(chǎn)普通碳素鋼就無需通過添加鐵水來提升電爐相關(guān)經(jīng)濟(jì)技術(shù)指標(biāo),但在電弧爐冶煉部分高品質(zhì)特殊鋼品種時仍需添加鐵水的方式來稀釋鋼液中有害雜質(zhì)元素。
2
電弧爐綠色化生產(chǎn)技術(shù)
電弧爐綠色化生產(chǎn)主要是為了降低能源消耗、減少污染物排放以及提升資源循環(huán)利用效率。為實(shí)現(xiàn)電弧爐綠色化生產(chǎn),相繼研發(fā)了余熱回收、焦炭替代、二英防治以及廢鋼預(yù)熱-連續(xù)加料等關(guān)鍵技術(shù)。
2.1余熱回收技術(shù)
電弧爐冶煉過程中會產(chǎn)生大量的高溫含塵煙氣,其帶走熱量約為電弧爐輸入總能量的11%,*高可達(dá)20%,因此,電弧爐煉鋼過程中余熱回收對節(jié)能降耗具有重要意義,同時也具備巨大經(jīng)濟(jì)效益。
特諾恩(Tenova)公司研發(fā)的iRecovery技術(shù)將電弧爐產(chǎn)生的高溫?zé)煔庥酂徂D(zhuǎn)換成蒸汽,iRecoveryStage2系統(tǒng)流程如圖3所示。iRecovery技術(shù)基于與傳統(tǒng)熱回收系統(tǒng)相似的管-管式熱交換結(jié)構(gòu)和工作原理,利用冷卻水從電弧爐廢氣管道回收熱能;與傳統(tǒng)熱回收系統(tǒng)不同之處在于iRecovery技術(shù)使用了高壓和高溫?zé)崴?180~250 ℃)作為熱交換介質(zhì)回收高溫含塵廢氣熱量,從而降低了蒸發(fā)分離廢氣導(dǎo)致的熱損失。
近年來,全世界范圍內(nèi)有多座電弧爐采用了iRecovery余熱回收技術(shù),如韓國現(xiàn)代、中國天津鋼管等企業(yè),該技術(shù)工業(yè)應(yīng)用*良好。一些典型企業(yè)電弧爐采用余熱回收技術(shù)的使用*見表6。
2.2焦炭替代技術(shù)
傳統(tǒng)電弧爐冶煉過程中為了滿足熔池升溫及攪拌和造泡沫渣埋弧的要求,需要進(jìn)行配碳。在電弧爐綠色化生產(chǎn)中,應(yīng)盡可能減少不可再生的化石能源如焦炭等消耗。目前減少焦炭消耗的方法之一是使用可替代燃料,如使用日常生活循環(huán)過程中產(chǎn)生的“廢料”,如橡膠輪胎和塑料制品等,此類“廢料”不僅可以成為電弧爐煉鋼的優(yōu)良替代品,還可避免“廢料”堆積導(dǎo)致的環(huán)保問題。
澳大利亞Onesteel鋼鐵公司與新南威爾士大學(xué)(UNSW)在Sydney Steel Mill(SSM)和Laverton Steel Mill(LSM)鋼廠完成了一系列利用橡膠和塑料部分代替焦炭作為造泡沫渣發(fā)泡劑的電弧爐煉鋼工業(yè)試驗(yàn)。SSM和LSM鋼廠使用高分子聚乙烯噴射技術(shù)(PIT),將橡膠與焦炭的混合料噴射進(jìn)入電弧爐內(nèi),其*優(yōu)于單純使用焦炭造渣*,相關(guān)指標(biāo)變化見表7。同時,Onesteel鋼鐵公司在LSM鋼廠進(jìn)行了將高分子聚合物和*等制成小塊來替代焦炭的工業(yè)化試驗(yàn),結(jié)果表明,噸鋼電耗下降10 kW·h,每爐次通電時間平均縮短1.2 min,有效功率增加0.4 MW。電弧爐采用廢棄輪胎和廢棄塑料煉鋼,能有效降低焦炭消耗,提高電弧爐熱效率和生產(chǎn)率,同時提升資源循環(huán)利用率,具有明顯的經(jīng)濟(jì)效益和社會效益。
2.3二英防治技術(shù)
二英具有超長的物理、化學(xué)、生物學(xué)降解期,導(dǎo)致其在水體沉淀物和食物鏈中達(dá)到非常高的含量;二英通過食物鏈進(jìn)入人體后,會嚴(yán)重?fù)p害人體系統(tǒng),如內(nèi)分泌、免疫、神經(jīng)系統(tǒng)等,其被稱為“毒素傳遞素”。二英對環(huán)境和人類危害巨大。
防治二英污染問題已成為冶金工業(yè)環(huán)境保護(hù)中極其重要課題之一。在鋼鐵工業(yè)生產(chǎn)過程中,除燒結(jié)工序以外,電弧爐煉鋼是產(chǎn)生二英的主要來源。根據(jù)Mckay G的研究,二英的形成需要具備兩個主要條件:一是在燃燒過程中必須有有機(jī)物;二是在燃燒反應(yīng)中必須有氯氣參與。關(guān)于二英的形成機(jī)理,Dickson L C、Gullett B K、Huang H、Hunisinger H、Takasuga T等做了一系列的研究,針對關(guān)于二英的形成條件已達(dá)成共識。由于廢鋼中通常含有氯化物和油類碳?xì)浠衔铮瑢?dǎo)致電弧爐冶煉過程中會產(chǎn)生一定量的二英煙氣,從而造成環(huán)境污染問題。
針對電弧爐煉鋼過程二英的排放問題,可采取以下主要措施。
(1)廢鋼預(yù)處理:對廢鋼進(jìn)行分選,*大限度減少含有有機(jī)物的廢鋼入爐量,同時嚴(yán)格控制進(jìn)入電弧爐的氯源總量;含有機(jī)物廢鋼不宜采取預(yù)熱處理。
(2)急冷處理一次煙氣:電弧爐一次煙氣溫度需控制在1000 ℃以上,此時各種有機(jī)物已經(jīng)全部分解,對燃燒后的煙氣進(jìn)行急冷,使其快速冷卻至200 ℃以下,*大限度減少煙氣在二英生成溫度區(qū)間的停留時間,如蒸發(fā)冷卻塔技術(shù)對煙氣急冷處理后,在防止二英形成方面*顯著。
(3)施加抑制劑:在600~800 ℃溫度區(qū)間向煙道噴入堿性物質(zhì)粉料(如石灰石或生石灰),可減少導(dǎo)致二英生成的有效氯源;在250~400 ℃噴入氨也可以抑制二英的生成。
日本開發(fā)的環(huán)保型生態(tài)電弧爐ECOARCTM(圖4)擁有較完善的廢氣排放處理系統(tǒng),能有效解決二英等環(huán)境污染問題。該電弧爐本體由廢鋼熔化室和與熔化室直接連接的預(yù)熱豎爐組成,后段設(shè)有熱分解燃燒室、直接噴霧冷卻室和除塵裝置。熱分解燃燒室可將包括二英在內(nèi)的有機(jī)廢氣全部分解,并能夠滿足高溫區(qū)煙氣的滯留時間;噴霧冷卻室可將高溫?zé)煔饪焖俳禍?,防止二英二次形成。但由于ECOARCTM電弧爐存在爐體體積大,豎井難以分離和耐火材料在線更換困難等問題,導(dǎo)致設(shè)備維護(hù)困難。因此,開發(fā)*率、低成本的電弧爐二英防治技術(shù)仍是目前的研究熱點(diǎn)之一。
2.4廢鋼預(yù)熱-連續(xù)加料技術(shù)
現(xiàn)代電弧爐煉鋼多采用廢鋼預(yù)熱-連續(xù)加料操作,利用高溫?zé)煔忸A(yù)熱廢鋼,能有效解決傳統(tǒng)電弧爐冶煉過程中的煙塵問題。另外,采取大留鋼量操作,廢鋼熔化效率高,*實(shí)現(xiàn)平熔池冶煉,滿足現(xiàn)代電弧爐煉鋼*率、高生產(chǎn)率、低成本、低有害氣體排放的要求。
在電弧爐廢鋼預(yù)熱-連續(xù)加料方面,先后開發(fā)并應(yīng)用了料籃式廢鋼預(yù)熱電弧爐、雙爐殼電弧爐、豎式電弧爐以及Consteel電弧爐等。料籃式廢鋼預(yù)熱電弧爐由于電耗高、冶煉周期長以及環(huán)境污染嚴(yán)重等問題,正逐步被新型電弧爐所取代;雙爐殼電弧爐由于預(yù)熱效率低、設(shè)備維護(hù)量大以及二英等污染物排放嚴(yán)重等問題,使用*遠(yuǎn)達(dá)不到預(yù)期,已經(jīng)逐漸被淘汰;Consteel電弧爐存在廢鋼預(yù)熱溫度較低、二英排放不達(dá)標(biāo)等問題,但其生產(chǎn)順行狀況良好、電網(wǎng)沖擊小、加料可靠可控等優(yōu)點(diǎn),目前使用較廣泛;早期豎式電弧爐存在設(shè)備可靠性低、維護(hù)量大等問題正逐步退出市場。當(dāng)前國內(nèi)外許多冶金設(shè)備制造公司依據(jù)Consteel電弧爐和豎式電弧爐理念研發(fā)了多種新型廢鋼預(yù)熱-連續(xù)加料電弧爐,如基于水平連續(xù)加料理念研發(fā)的達(dá)涅利FASTARC 0電弧爐;基于豎式加料理念研發(fā)的西馬克SHARC電弧爐、日本ECOARCTM生態(tài)電弧爐以及普瑞特Quantum電弧爐等;同時還衍出階梯進(jìn)料型電弧爐,如中冶賽迪CISDI-AutoARCTM綠色智能電弧爐,以及獨(dú)立于電弧爐的廢鋼預(yù)熱-連續(xù)加料系統(tǒng),如KR公司和CVS公司聯(lián)合研發(fā)的環(huán)保型爐料預(yù)熱和連續(xù)加料系統(tǒng)EPC(Environmental Pre-heating and Continuous Charging System)。
Consteel電弧爐(圖5)是在連續(xù)加料的同時利用冶煉產(chǎn)生的高溫廢氣對加料通道內(nèi)廢鋼進(jìn)行連續(xù)預(yù)熱,入爐前廢鋼預(yù)熱溫度為200~400 ℃;預(yù)熱后的廢氣經(jīng)燃燒室進(jìn)入預(yù)熱回收系統(tǒng)。Consteel電弧爐實(shí)現(xiàn)了廢鋼連續(xù)預(yù)熱、連續(xù)加料、連續(xù)熔化、平熔池冶煉,提升了生產(chǎn)率,改善了車間內(nèi)外的環(huán)保條件,降低了電耗及電極消耗等。
早期豎式電弧爐在冶煉的同時,用天車料籃在豎井中加入下一爐所需廢鋼,用指形托架托住廢鋼,高溫廢氣直接與廢鋼接觸預(yù)熱,廢鋼溫度高達(dá)600~700 ℃。SHARC電弧爐(圖6)屬于改進(jìn)型豎爐式電弧爐,其*大的特點(diǎn)是電弧爐上有2個半圓形豎井,能保持豎井內(nèi)高溫廢氣對廢鋼進(jìn)行自然對流預(yù)熱,熔池平穩(wěn),其加料方式仍采用天車料籃;ECOARCTM生態(tài)電弧爐(圖4)利用豎爐豎井預(yù)熱廢鋼,可實(shí)現(xiàn)輕薄型廢鋼的連續(xù)加料,預(yù)熱溫度超過600 ℃,熔池穩(wěn)定,生產(chǎn)率高;Quantum電弧爐(圖7)屬于改進(jìn)型指形托架豎爐式電弧爐,通過爐頂廢鋼提升機(jī)提升傾動料槽將廢鋼分批加入豎井內(nèi),固定安裝豎井和爐蓋解決了原指形托架故障多的缺點(diǎn),傾翻爐體實(shí)現(xiàn)無渣出鋼。
環(huán)保型爐料預(yù)熱和連續(xù)加料系統(tǒng)EPC(environmental pre-heating and continuous charging system)是豎井型爐料預(yù)熱裝置,與其匹配的電弧爐采取較大的留鋼操作工藝(出鋼量的40%以上),因此此類電弧爐能平穩(wěn)地連續(xù)運(yùn)行。爐料通過側(cè)墻加料口連續(xù)地加到爐中,無需打開爐蓋,避免了熱量損失和煙氣排放。EPC系統(tǒng)可移動到電弧爐的上爐殼附近,與電弧爐側(cè)墻加料口及排煙道之間實(shí)現(xiàn)緊密銜接。其具體工藝流程如圖8所示。
各典型電弧爐技術(shù)指標(biāo)及廢鋼預(yù)熱*的對比見表8。通過總結(jié)電弧爐*預(yù)熱特征,可知廢鋼預(yù)熱技術(shù)未來發(fā)展趨勢:(1)電弧爐冶煉過程中全程密封,避免開蓋造成熱損失;水平加料式電弧爐雖預(yù)熱*有待進(jìn)一步提升,但其加料可控可靠,設(shè)備穩(wěn)定好;豎式電弧爐廢鋼預(yù)熱效率高,近年來新型電弧爐多為豎式加料結(jié)構(gòu);(2)平衡各類能源輸入量,注重物理余熱與化學(xué)余熱輸入對提高廢鋼預(yù)熱效率的作用,進(jìn)而改進(jìn)能源利用率提高電弧爐產(chǎn)能;(3)廢鋼預(yù)熱技術(shù)設(shè)計(jì)理念應(yīng)符合*新環(huán)保標(biāo)準(zhǔn),減少能源消耗,減少溫室氣體排放;(4)新型電弧爐煉鋼需綜合考慮廢鋼預(yù)熱、連續(xù)加料、平熔池冶煉、余熱回收、廢氣處理等方面,保證電弧爐煉鋼*、綠色化生產(chǎn)。
3
電弧爐智能化控制技術(shù)
近年來,一系列智能化監(jiān)測技術(shù)和控制模型在電弧爐煉鋼過程中得到應(yīng)用,如智能配料、電極智能調(diào)控、智能化取樣測溫、泡沫渣智能化監(jiān)測與控制、爐氣在線分析、終點(diǎn)成分預(yù)報(bào)、冶煉過程成本優(yōu)化和電弧爐煉鋼過程整體智能控制等,監(jiān)測和控制技術(shù)的應(yīng)用大幅度提高了電弧爐煉鋼過程的智能化水平。
3.1電極智能調(diào)節(jié)控制技術(shù)
電極調(diào)節(jié)控制技術(shù)是電弧爐實(shí)現(xiàn)智能化供電關(guān)鍵技術(shù)之一,其控制*直接影響電弧爐的電能消耗、冶煉周期等重要經(jīng)濟(jì)性能指標(biāo)。近年來,國際上較為成熟的智能電弧爐電極調(diào)節(jié)控制技術(shù)主要有3種:美國的IAFTM和SmartArcTM、德國的SimeltRNEC系統(tǒng)。國際典型電弧爐電極調(diào)節(jié)控制系統(tǒng)的技術(shù)對比見表9。
目前,基于PLC和工業(yè)計(jì)算機(jī)硬件平臺研發(fā)的SIMETAL電極控制系統(tǒng)是*新的電弧爐智能化電極控制系統(tǒng),圖9所示為SIMETAL Simelt系統(tǒng),該控制系統(tǒng)能根據(jù)實(shí)際工藝需求作出動態(tài)響應(yīng),提高工藝效率。在此基礎(chǔ)上,下一代電極控制系統(tǒng)的研發(fā)主要集中在過程參數(shù)及算法自適應(yīng),數(shù)據(jù)記錄、數(shù)據(jù)評估及集成過程可視化,可靠性高等方面。
3.2電弧爐智能化取樣測溫
電弧爐煉鋼過程中鋼液溫度測量和取樣所消耗的時間等是制約電弧爐電能消耗和生產(chǎn)效率的關(guān)鍵環(huán)節(jié)之一。針對傳統(tǒng)人工測溫取樣安全性差、成本高等問題,開發(fā)并推廣應(yīng)用一系列自動化測溫取樣新技術(shù)。目前較先進(jìn)的測溫方式是機(jī)器人全自動測溫和非接觸式測溫。
奧鋼聯(lián)推出的SIMETAL LiquiROB電弧爐機(jī)器人(圖10)能執(zhí)行全自動測溫和取樣操作,能自動更換取樣器和測溫探頭以及檢測無效測溫探頭等,同時還能通過人機(jī)界面實(shí)現(xiàn)全自動控制。
SIMETAL RCB Temp(圖11)是奧鋼聯(lián)開發(fā)的一種非接觸式溫度測量系統(tǒng),其依靠超音速氧氣射流技術(shù),在加料期間對廢鋼進(jìn)行預(yù)熱,加快廢鋼熔化速度,在精煉期以超音速射流噴吹氧氣,一旦達(dá)到規(guī)定的溫度均勻性水平,系統(tǒng)切換到溫度模式,以極短的時間間隔對溫度進(jìn)行分析。
3.3泡沫渣智能化監(jiān)測與控制
電弧爐的泡沫渣工藝主要通過目視觀察和人工噴碳操作相結(jié)合的方式進(jìn)行?;陔娏餍盘柡椭C波含量的半自動系統(tǒng)只能在一定程度上協(xié)助操作人員完成泡沫渣工藝過程。優(yōu)化泡沫渣智能化監(jiān)測與控制方案,確保電弧和熔池完全被泡沫渣穩(wěn)定地覆蓋,既能節(jié)約資源和降低電耗,也有利于降低生產(chǎn)成本和減少熱損失,是冶煉工藝實(shí)現(xiàn)全自動運(yùn)行的重要方面。
Siemens開發(fā)的Simelt SonArc FSM 泡沫渣監(jiān)控系統(tǒng)(圖12)保證了泡沫渣工藝的全自動進(jìn)行,聲音傳感器為精確監(jiān)測和分析泡沫渣高度奠定了基礎(chǔ);同時,泡沫渣高度的監(jiān)測為自動噴碳操作提供指導(dǎo),從而*大限度降低消耗指標(biāo)。
美國PTI 公司開發(fā)的電弧爐爐門清掃和泡沫渣控制系統(tǒng)PTI SwingDoorTM(圖13)能減少外界空氣的進(jìn)入,提高煉鋼過程的密封性;其集成氧槍系統(tǒng)代替了爐門清掃機(jī)械手或爐門氧槍自動清掃爐門區(qū)域。該系統(tǒng)通過控制爐門開合控制流渣,實(shí)現(xiàn)控制爐內(nèi)泡沫渣存在時間,進(jìn)而保證冶煉過程中爐膛內(nèi)渣層的厚度,減少能源消耗,提高電弧傳熱效率。
3.4電弧爐煉鋼過程整體智能控制
電弧爐智能化控制并非局限于某一設(shè)備的自動化、某一環(huán)節(jié)監(jiān)測與控制的智能化,而是從整體電弧爐煉鋼出發(fā),從*初配料到*終出鋼整個冶煉過程的數(shù)據(jù)采集與過程機(jī)理和工藝操作相結(jié)合,進(jìn)行數(shù)據(jù)分析、數(shù)據(jù)決策、數(shù)據(jù)評估以及*后流程控制,實(shí)現(xiàn)電弧爐煉鋼過程整體優(yōu)化,減少人為干預(yù),以此達(dá)到電弧爐煉鋼過程整體智能控制。
達(dá)涅利Q-Melt自動電弧爐系統(tǒng)(圖14)集成了過程控制監(jiān)視器和管理器,可自動識別電弧爐煉鋼過程預(yù)期行為的偏差,并使其自動返回到預(yù)定的冶煉過程。此系統(tǒng)主要包括Q-REG Plus電極動態(tài)調(diào)節(jié)控制系統(tǒng)、LINDARC廢氣分析系統(tǒng)和MELT-MODEL過程控制和優(yōu)化系統(tǒng)。其中MELT-MODEL過程控制和優(yōu)化系統(tǒng)是Q-MELT系統(tǒng)核心,與電極調(diào)節(jié)系統(tǒng)和廢氣分析系統(tǒng)相配合,通過化學(xué)成分分析或電氣特性曲線進(jìn)行動態(tài)調(diào)整電弧爐冶煉工藝,使冶煉過程始終保持*佳工藝狀態(tài)。
Tenova開發(fā)的iEAF智能控制系統(tǒng)(圖15)依靠傳感器反饋的工藝信息(如廢氣分析、電諧波、電流和電壓)和可控參數(shù)(氧氣和燃料流量、氧氣噴吹、*噴吹和電極管理)對電弧爐進(jìn)行*控制。此系統(tǒng)通過減少冶煉操作變數(shù),增強(qiáng)電弧爐運(yùn)行穩(wěn)定性從而提高生產(chǎn)效率、改善生產(chǎn)管理、節(jié)能降耗和減少CO2排放。
4
結(jié)論與展望
電弧爐煉鋼在“節(jié)能降耗、提高生產(chǎn)率”思想指導(dǎo)下,開發(fā)了諸多*化冶煉、綠色化生產(chǎn)和智能化控制方面技術(shù),并且綠色化和智能化技術(shù)在電弧爐煉鋼未來發(fā)展中的重要性將日益突出。未來電弧爐煉鋼將進(jìn)一步優(yōu)化基于配料、供電、供氧、輔助能源輸入、造渣等全流程電弧爐智能化監(jiān)測及控制模型和整體智能控制模型,開發(fā)低能源消耗、少污染物排放以及資源循環(huán)利用的綠色化生產(chǎn)技術(shù),完善集操作、工藝、質(zhì)量、成本、環(huán)保等于一體的電弧爐煉鋼流程,*終實(shí)現(xiàn)電弧爐綠色、智能、*和低成本煉鋼的目標(biāo),進(jìn)一步推動鋼鐵工業(yè)轉(zhuǎn)型升級。
5
參考文獻(xiàn)
略。
6
引用本文
姜周華, 姚聰林, 朱紅春, 潘濤. 電弧爐煉鋼技術(shù)的發(fā)展趨勢[J]. 鋼鐵, 2020, 55(7): 1-12. JIANG Zhou-hua, YAO Cong-lin, ZHU Hong-chun, PAN Tao. Technology development trend in electric arc furnace steelmaking[J]. Iron and Steel, 2020, 55(7): 1-12.
7
免費(fèi)下載全文鏈接
https://p3.itc.cn/q_70/images03/20230823/1b8cf86a69be4c31b5f8ecdddc1bd097.png8"font-size: 16px;"> 來源:《鋼鐵》2020年第7期
END
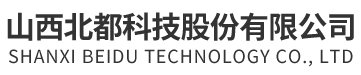
服務(wù)熱線:0359-5668082
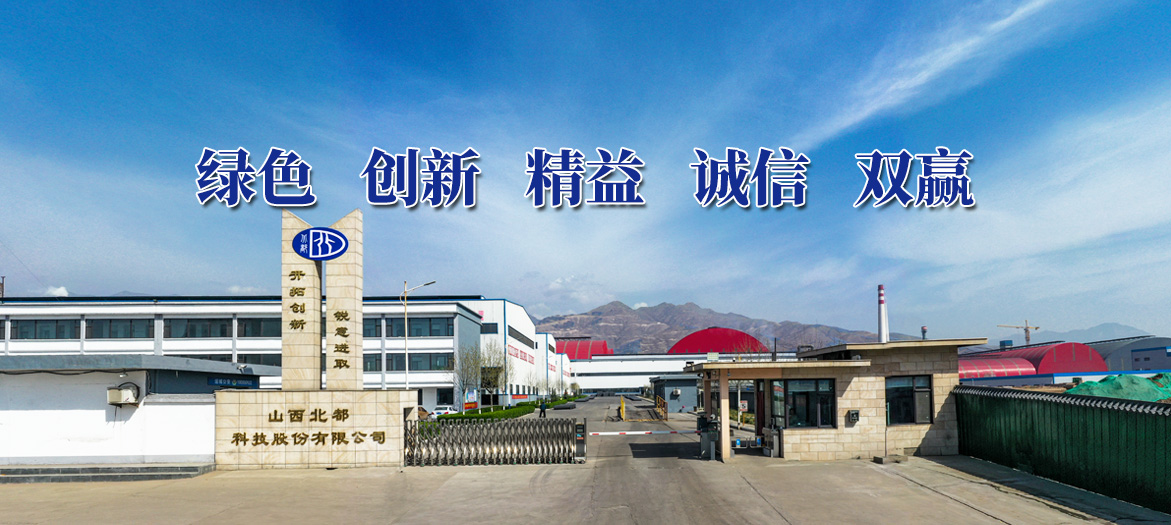
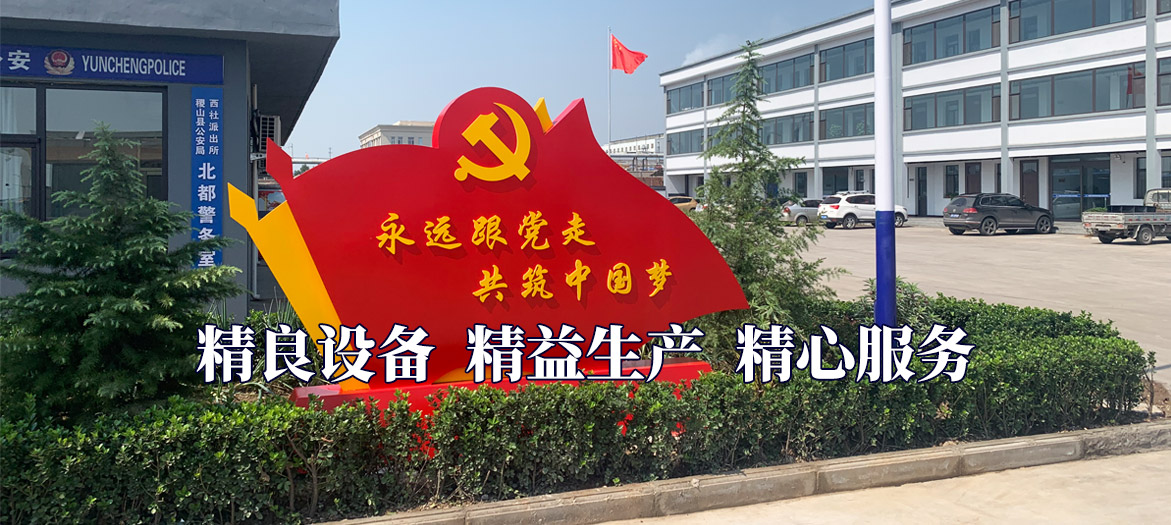
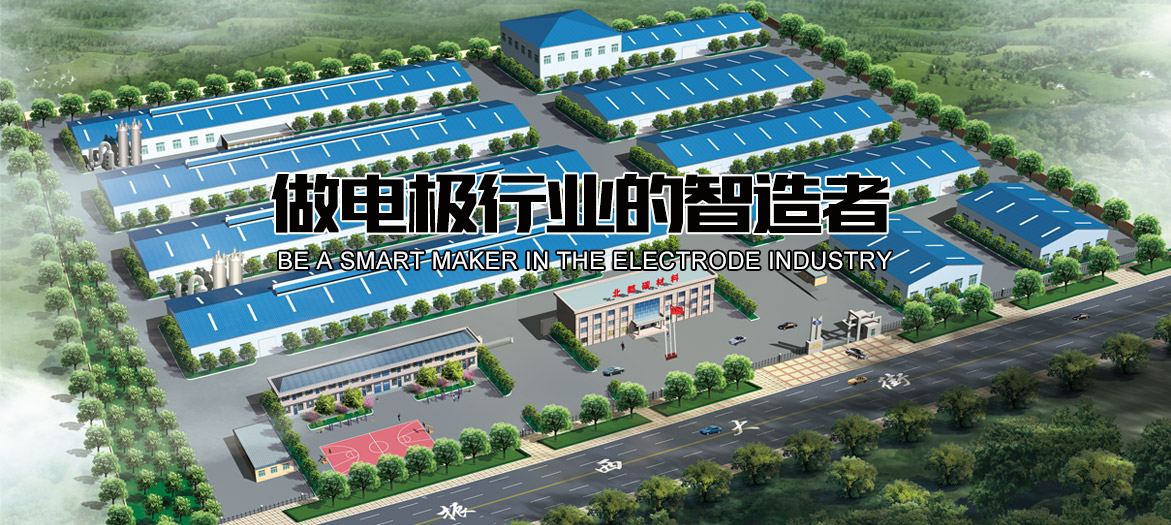
文章詳情 DETAILS
文章詳情 DETAILS
【“三高”論文推薦】姜周華:電弧爐煉鋼技術(shù)的發(fā)展趨勢
編輯:2023-10-30 16:07:46
電弧爐煉鋼技術(shù)的發(fā)展趨勢
姜周華1,2,姚聰林1,朱紅春1,潘濤1
(1. 東北大學(xué)冶金學(xué)院, 遼寧 沈陽 110819;2. 東北大學(xué)軋制技術(shù)及連軋自動化國家重點(diǎn)實(shí)驗(yàn)室, 遼寧 沈陽 110819)
摘要:電弧爐煉鋼在環(huán)保、投資以及效率方面優(yōu)勢明顯,為了重點(diǎn)推行該節(jié)能環(huán)保型煉鋼工藝流程,近年來電弧爐煉鋼技術(shù)得到快速發(fā)展。綜述了國內(nèi)外電弧爐*化冶煉技術(shù)、綠色化生產(chǎn)技術(shù)和智能化控制技術(shù)的發(fā)展現(xiàn)狀,其中綠色化和智能化是電弧爐煉鋼技術(shù)的未來發(fā)展趨勢。集操作、工藝、質(zhì)量、成本以及環(huán)保于一體,進(jìn)一步提升電弧爐煉鋼技術(shù)的綠色化和全流程監(jiān)測與控制的智能化,是推動整個鋼鐵行業(yè)向智能化和綠色化轉(zhuǎn)型升級的重要舉措。
關(guān)鍵詞:電弧爐煉鋼; 廢鋼預(yù)熱; *化; 綠色化; 智能化
電弧爐是一種利用電弧熱效應(yīng),將電能轉(zhuǎn)變?yōu)闊崮?,并通過輻射和電弧直接作用加熱并熔化金屬的設(shè)備;電弧爐煉鋼在環(huán)保、投資以及效率上占據(jù)諸多優(yōu)勢。在全球范圍內(nèi)電爐鋼產(chǎn)量占鋼總產(chǎn)量比例已從20世紀(jì)50年代初的7.3%提高到32%~35%。2018年全球電爐鋼平均占比為28.8%,其中美國為68%、歐盟為41.5%、日本為25%,而中國僅約為11.6%,明顯低于平均水平,較低的電爐鋼比例是造成鋼鐵工業(yè)能耗高、污染大的重要原因之一。目前,全球范圍內(nèi)95%以上電爐鋼產(chǎn)量是由電弧爐生產(chǎn)制備的,以電弧爐煉鋼為核心的短流程煉鋼已經(jīng)成為整個鋼鐵生產(chǎn)的重要流程之一?!白⒅匾詮U鋼為原料的短流程電爐煉鋼發(fā)展”是實(shí)現(xiàn)鋼鐵工業(yè)可持續(xù)發(fā)展的重大戰(zhàn)略決策之一。
縱觀發(fā)展歷程,電弧爐煉鋼圍繞著“節(jié)能降耗、提高生產(chǎn)率”的總體目標(biāo),研發(fā)了一系列相關(guān)技術(shù)。20世紀(jì)60-70年代,電弧爐煉鋼技術(shù)的發(fā)展以提升生產(chǎn)率為主導(dǎo),開發(fā)了超高功率電弧爐及相關(guān)技術(shù);80-90年代,強(qiáng)化用氧技術(shù)趨于成熟;為了進(jìn)一步節(jié)能降耗、縮短冶煉周期,廢氣的余熱利用逐步受到重視,并研發(fā)了一系列廢鋼預(yù)熱技術(shù),如料籃式、雙爐殼式、豎爐式以及水平連續(xù)加料式等。與此同時,環(huán)境保護(hù)意識的加強(qiáng)及人工智能技術(shù)的快速發(fā)展,對電弧爐煉鋼技術(shù)提出了新要求,指明了新發(fā)展方向。電弧爐煉鋼技術(shù)融合了各種現(xiàn)代裝備及其配套技術(shù)的綜合技術(shù),在*化冶煉基礎(chǔ)上,智能化及綠色化是電弧爐未來發(fā)展方向。本文通過綜述近年來電弧爐煉鋼技術(shù)發(fā)展現(xiàn)狀,探討了電弧爐煉鋼技術(shù)的未來發(fā)展方向。
1
電弧爐*化冶煉技術(shù)
電弧爐*化生產(chǎn)具備全局協(xié)同、連續(xù)化生產(chǎn)等特點(diǎn)。電弧爐冶煉工藝*化的目標(biāo)是減少通電時長、縮短冶煉周期以及*大限度降低冶煉電耗;具體措施主要包括提升功率、提高化學(xué)能輸入強(qiáng)度和減少非通電操作時間等。
1.1電弧爐爐容大型化
生產(chǎn)實(shí)踐證明,在技術(shù)經(jīng)濟(jì)指標(biāo)方面(如冶煉用電、電極單耗以及成本等),大型電弧爐的生產(chǎn)率及能源利用率均高于中小型電弧爐。目前,電弧爐正朝著爐容大型化方向發(fā)展。工業(yè)發(fā)達(dá)國家主流電弧爐容量為80~150 t,且已逐步增至150~200 t。如意大利達(dá)涅利公司(DANIELI)成功制造了全球*大爐容量為420 t的直流電弧爐,如圖1所示,該電弧爐設(shè)計(jì)生產(chǎn)率為360 t/h,具有*率、低運(yùn)行成本的特點(diǎn),能提升鋼廠生產(chǎn)效率和鋼的品質(zhì);已用于生產(chǎn)低碳鋼、超低碳鋼和高級脫氧*鋼,年產(chǎn)量為260萬t。
根據(jù)中國工業(yè)和信息化部等相關(guān)部門統(tǒng)計(jì),2015年中國電弧爐分噸位生產(chǎn)能力比例如圖2所示;國內(nèi)100 t及以上的大容量電弧爐產(chǎn)能占電弧爐煉鋼總產(chǎn)能的30.8%,占比*高;75 t及以上電弧爐產(chǎn)能占電弧爐煉鋼總產(chǎn)能的56.6%。此外,60 t以下的落后產(chǎn)能還有21.9%,這表明在環(huán)保限產(chǎn)和淘汰落后產(chǎn)能政策引導(dǎo)下,國內(nèi)鋼廠在通過產(chǎn)能置換提升電弧爐效率方面仍存在較大空間。
2018年國內(nèi)新增電弧爐中70~120 t公稱容積所占比例為80%。中國電弧爐正朝著裝備大型化和現(xiàn)代化快速發(fā)展,但與工業(yè)發(fā)達(dá)國家之間仍存在較大差距。
1.2超高功率供電技術(shù)
根據(jù)供電功率大小,電弧爐變壓器可分為普通功率(RP)、高功率(HP)和超高功率(UHP) 3類。從20世紀(jì)60年代至今,超高功率電弧爐煉鋼的理念主導(dǎo)了近60年電弧爐煉鋼生產(chǎn)技術(shù)的發(fā)展,其核心思想是*大限度地發(fā)揮主變壓器能力。大功率電弧爐變壓器是滿足電弧爐煉鋼*化、實(shí)現(xiàn)超高功率供電的基礎(chǔ)。制造商制造100 t電弧爐變壓器的主要參數(shù)及技術(shù)經(jīng)濟(jì)指標(biāo)見表1。
要實(shí)現(xiàn)超高功率供電,起協(xié)調(diào)電力波動和穩(wěn)定電弧作用的科學(xué)合理供電制度尤為重要。墨西哥泰納Tamsa鋼廠為優(yōu)化供電制度,在2016年和2017年期間開發(fā)并應(yīng)用了具備修改和優(yōu)化電弧爐供電制度功能的模型,該模型基于能量平衡(電能/化學(xué)能)、通電時間、電弧穩(wěn)定性、輻射指數(shù)等參數(shù)變化規(guī)律自動優(yōu)化供電曲線。Tamsa鋼廠利用此模型重新設(shè)計(jì)供電制度,在保持能耗水平基本不變的情況下,電弧爐產(chǎn)能提高了9.8%,生產(chǎn)率提升*明顯。
采用超高功率供電后的主要優(yōu)點(diǎn)有:縮短冶煉時間,提高生產(chǎn)效率;提高電熱效率,降低電耗;易與精煉、連鑄的生產(chǎn)節(jié)奏相匹配,從而實(shí)現(xiàn)*低耗生產(chǎn)。70 t電弧爐超高功率改造后,生產(chǎn)率由27提升至62 t/h,見表2。
1.3熔池?cái)嚢杓杉夹g(shù)
傳統(tǒng)電弧爐煉鋼熔池?cái)嚢鑿?qiáng)度較弱,爐內(nèi)物質(zhì)和能量傳遞較慢。采用超高功率供電、高強(qiáng)度化學(xué)能輸入等技術(shù),也未從根本上解決熔池?cái)嚢鑿?qiáng)度不 足和物質(zhì)能量傳遞速度慢等問題。為加快冶煉節(jié)奏,相繼研發(fā)了強(qiáng)化供氧和底吹攪拌等復(fù)合吹煉技術(shù),以及電磁攪拌技術(shù)等。新一代電弧爐熔池?cái)嚢杓夹g(shù)是集強(qiáng)化供氧、底吹攪拌及電磁攪拌等單元于一體,能滿足多元爐料條件下電弧爐冶煉的技術(shù)要求。
電弧爐煉鋼復(fù)合吹煉技術(shù)日趨成熟,已實(shí)現(xiàn)了工業(yè)推廣應(yīng)用,如中國的西寧特鋼、天津鋼管、新余特鋼、衡陽鋼管等企業(yè)均成功應(yīng)用了電弧爐煉鋼復(fù)合吹煉工藝,工業(yè)*良好,有效地降低了成本。中國部分電弧爐復(fù)合吹煉技術(shù)改造前后的工業(yè)*對比見表3。
與復(fù)合吹煉技術(shù)相比,電弧爐電磁攪拌技術(shù)普及面較窄,但其熔池?cái)嚢?更加優(yōu)異,工業(yè)應(yīng)用*反響良好。以ABB研發(fā)的電磁攪拌設(shè)備(ArcSave)為例,電磁攪拌技術(shù)有效提升了熔池中物質(zhì)和能量傳遞速率,更有利于廢鋼熔化,加速均勻鋼水成分及溫度,提高電弧爐產(chǎn)能。Steel Dynamics Inc(SDI)Roanode電弧爐ArcSave改造后相關(guān)指標(biāo)提升*,見表4。
1.4熱裝鐵水技術(shù)
由于電力資源的緊張和優(yōu)質(zhì)廢鋼資源的短缺,近年來,部分電弧爐煉鋼廠煉鋼過程中添加一定量鐵水,即鐵水熱裝的電弧爐煉鋼工藝,該工藝有效縮短電弧爐冶煉周期,同時幫助企業(yè)靈活應(yīng)對廢鋼市場價格波動,具備一定經(jīng)濟(jì)效益。
采用熱裝鐵水技術(shù)在電弧爐煉鋼過程應(yīng)用較普遍,如中國的中天鋼鐵公司和天津鋼鐵公司等,其中達(dá)涅利連續(xù)加料電弧爐(EAF ECS)為滿足添加鐵水的需要,對電弧爐進(jìn)行了特殊設(shè)計(jì)和改造。國內(nèi)某鋼廠的電弧爐熱裝鐵水后的電弧爐經(jīng)濟(jì)技術(shù)指標(biāo)見表5。實(shí)踐表明,現(xiàn)代電弧爐熱裝鐵水對于縮短冶煉周期、降低電耗等*非常顯著。
從長遠(yuǎn)來看,當(dāng)廢鋼冶煉成本與轉(zhuǎn)爐冶煉相當(dāng)或具備一定競爭力時,電弧爐冶煉生產(chǎn)普通碳素鋼就無需通過添加鐵水來提升電爐相關(guān)經(jīng)濟(jì)技術(shù)指標(biāo),但在電弧爐冶煉部分高品質(zhì)特殊鋼品種時仍需添加鐵水的方式來稀釋鋼液中有害雜質(zhì)元素。
2
電弧爐綠色化生產(chǎn)技術(shù)
電弧爐綠色化生產(chǎn)主要是為了降低能源消耗、減少污染物排放以及提升資源循環(huán)利用效率。為實(shí)現(xiàn)電弧爐綠色化生產(chǎn),相繼研發(fā)了余熱回收、焦炭替代、二英防治以及廢鋼預(yù)熱-連續(xù)加料等關(guān)鍵技術(shù)。
2.1余熱回收技術(shù)
電弧爐冶煉過程中會產(chǎn)生大量的高溫含塵煙氣,其帶走熱量約為電弧爐輸入總能量的11%,*高可達(dá)20%,因此,電弧爐煉鋼過程中余熱回收對節(jié)能降耗具有重要意義,同時也具備巨大經(jīng)濟(jì)效益。
特諾恩(Tenova)公司研發(fā)的iRecovery技術(shù)將電弧爐產(chǎn)生的高溫?zé)煔庥酂徂D(zhuǎn)換成蒸汽,iRecoveryStage2系統(tǒng)流程如圖3所示。iRecovery技術(shù)基于與傳統(tǒng)熱回收系統(tǒng)相似的管-管式熱交換結(jié)構(gòu)和工作原理,利用冷卻水從電弧爐廢氣管道回收熱能;與傳統(tǒng)熱回收系統(tǒng)不同之處在于iRecovery技術(shù)使用了高壓和高溫?zé)崴?180~250 ℃)作為熱交換介質(zhì)回收高溫含塵廢氣熱量,從而降低了蒸發(fā)分離廢氣導(dǎo)致的熱損失。
近年來,全世界范圍內(nèi)有多座電弧爐采用了iRecovery余熱回收技術(shù),如韓國現(xiàn)代、中國天津鋼管等企業(yè),該技術(shù)工業(yè)應(yīng)用*良好。一些典型企業(yè)電弧爐采用余熱回收技術(shù)的使用*見表6。
2.2焦炭替代技術(shù)
傳統(tǒng)電弧爐冶煉過程中為了滿足熔池升溫及攪拌和造泡沫渣埋弧的要求,需要進(jìn)行配碳。在電弧爐綠色化生產(chǎn)中,應(yīng)盡可能減少不可再生的化石能源如焦炭等消耗。目前減少焦炭消耗的方法之一是使用可替代燃料,如使用日常生活循環(huán)過程中產(chǎn)生的“廢料”,如橡膠輪胎和塑料制品等,此類“廢料”不僅可以成為電弧爐煉鋼的優(yōu)良替代品,還可避免“廢料”堆積導(dǎo)致的環(huán)保問題。
澳大利亞Onesteel鋼鐵公司與新南威爾士大學(xué)(UNSW)在Sydney Steel Mill(SSM)和Laverton Steel Mill(LSM)鋼廠完成了一系列利用橡膠和塑料部分代替焦炭作為造泡沫渣發(fā)泡劑的電弧爐煉鋼工業(yè)試驗(yàn)。SSM和LSM鋼廠使用高分子聚乙烯噴射技術(shù)(PIT),將橡膠與焦炭的混合料噴射進(jìn)入電弧爐內(nèi),其*優(yōu)于單純使用焦炭造渣*,相關(guān)指標(biāo)變化見表7。同時,Onesteel鋼鐵公司在LSM鋼廠進(jìn)行了將高分子聚合物和*等制成小塊來替代焦炭的工業(yè)化試驗(yàn),結(jié)果表明,噸鋼電耗下降10 kW·h,每爐次通電時間平均縮短1.2 min,有效功率增加0.4 MW。電弧爐采用廢棄輪胎和廢棄塑料煉鋼,能有效降低焦炭消耗,提高電弧爐熱效率和生產(chǎn)率,同時提升資源循環(huán)利用率,具有明顯的經(jīng)濟(jì)效益和社會效益。
2.3二英防治技術(shù)
二英具有超長的物理、化學(xué)、生物學(xué)降解期,導(dǎo)致其在水體沉淀物和食物鏈中達(dá)到非常高的含量;二英通過食物鏈進(jìn)入人體后,會嚴(yán)重?fù)p害人體系統(tǒng),如內(nèi)分泌、免疫、神經(jīng)系統(tǒng)等,其被稱為“毒素傳遞素”。二英對環(huán)境和人類危害巨大。
防治二英污染問題已成為冶金工業(yè)環(huán)境保護(hù)中極其重要課題之一。在鋼鐵工業(yè)生產(chǎn)過程中,除燒結(jié)工序以外,電弧爐煉鋼是產(chǎn)生二英的主要來源。根據(jù)Mckay G的研究,二英的形成需要具備兩個主要條件:一是在燃燒過程中必須有有機(jī)物;二是在燃燒反應(yīng)中必須有氯氣參與。關(guān)于二英的形成機(jī)理,Dickson L C、Gullett B K、Huang H、Hunisinger H、Takasuga T等做了一系列的研究,針對關(guān)于二英的形成條件已達(dá)成共識。由于廢鋼中通常含有氯化物和油類碳?xì)浠衔?,?dǎo)致電弧爐冶煉過程中會產(chǎn)生一定量的二英煙氣,從而造成環(huán)境污染問題。
針對電弧爐煉鋼過程二英的排放問題,可采取以下主要措施。
(1)廢鋼預(yù)處理:對廢鋼進(jìn)行分選,*大限度減少含有有機(jī)物的廢鋼入爐量,同時嚴(yán)格控制進(jìn)入電弧爐的氯源總量;含有機(jī)物廢鋼不宜采取預(yù)熱處理。
(2)急冷處理一次煙氣:電弧爐一次煙氣溫度需控制在1000 ℃以上,此時各種有機(jī)物已經(jīng)全部分解,對燃燒后的煙氣進(jìn)行急冷,使其快速冷卻至200 ℃以下,*大限度減少煙氣在二英生成溫度區(qū)間的停留時間,如蒸發(fā)冷卻塔技術(shù)對煙氣急冷處理后,在防止二英形成方面*顯著。
(3)施加抑制劑:在600~800 ℃溫度區(qū)間向煙道噴入堿性物質(zhì)粉料(如石灰石或生石灰),可減少導(dǎo)致二英生成的有效氯源;在250~400 ℃噴入氨也可以抑制二英的生成。
日本開發(fā)的環(huán)保型生態(tài)電弧爐ECOARCTM(圖4)擁有較完善的廢氣排放處理系統(tǒng),能有效解決二英等環(huán)境污染問題。該電弧爐本體由廢鋼熔化室和與熔化室直接連接的預(yù)熱豎爐組成,后段設(shè)有熱分解燃燒室、直接噴霧冷卻室和除塵裝置。熱分解燃燒室可將包括二英在內(nèi)的有機(jī)廢氣全部分解,并能夠滿足高溫區(qū)煙氣的滯留時間;噴霧冷卻室可將高溫?zé)煔饪焖俳禍?,防止二英二次形成。但由于ECOARCTM電弧爐存在爐體體積大,豎井難以分離和耐火材料在線更換困難等問題,導(dǎo)致設(shè)備維護(hù)困難。因此,開發(fā)*率、低成本的電弧爐二英防治技術(shù)仍是目前的研究熱點(diǎn)之一。
2.4廢鋼預(yù)熱-連續(xù)加料技術(shù)
現(xiàn)代電弧爐煉鋼多采用廢鋼預(yù)熱-連續(xù)加料操作,利用高溫?zé)煔忸A(yù)熱廢鋼,能有效解決傳統(tǒng)電弧爐冶煉過程中的煙塵問題。另外,采取大留鋼量操作,廢鋼熔化效率高,*實(shí)現(xiàn)平熔池冶煉,滿足現(xiàn)代電弧爐煉鋼*率、高生產(chǎn)率、低成本、低有害氣體排放的要求。
在電弧爐廢鋼預(yù)熱-連續(xù)加料方面,先后開發(fā)并應(yīng)用了料籃式廢鋼預(yù)熱電弧爐、雙爐殼電弧爐、豎式電弧爐以及Consteel電弧爐等。料籃式廢鋼預(yù)熱電弧爐由于電耗高、冶煉周期長以及環(huán)境污染嚴(yán)重等問題,正逐步被新型電弧爐所取代;雙爐殼電弧爐由于預(yù)熱效率低、設(shè)備維護(hù)量大以及二英等污染物排放嚴(yán)重等問題,使用*遠(yuǎn)達(dá)不到預(yù)期,已經(jīng)逐漸被淘汰;Consteel電弧爐存在廢鋼預(yù)熱溫度較低、二英排放不達(dá)標(biāo)等問題,但其生產(chǎn)順行狀況良好、電網(wǎng)沖擊小、加料可靠可控等優(yōu)點(diǎn),目前使用較廣泛;早期豎式電弧爐存在設(shè)備可靠性低、維護(hù)量大等問題正逐步退出市場。當(dāng)前國內(nèi)外許多冶金設(shè)備制造公司依據(jù)Consteel電弧爐和豎式電弧爐理念研發(fā)了多種新型廢鋼預(yù)熱-連續(xù)加料電弧爐,如基于水平連續(xù)加料理念研發(fā)的達(dá)涅利FASTARC 0電弧爐;基于豎式加料理念研發(fā)的西馬克SHARC電弧爐、日本ECOARCTM生態(tài)電弧爐以及普瑞特Quantum電弧爐等;同時還衍出階梯進(jìn)料型電弧爐,如中冶賽迪CISDI-AutoARCTM綠色智能電弧爐,以及獨(dú)立于電弧爐的廢鋼預(yù)熱-連續(xù)加料系統(tǒng),如KR公司和CVS公司聯(lián)合研發(fā)的環(huán)保型爐料預(yù)熱和連續(xù)加料系統(tǒng)EPC(Environmental Pre-heating and Continuous Charging System)。
Consteel電弧爐(圖5)是在連續(xù)加料的同時利用冶煉產(chǎn)生的高溫廢氣對加料通道內(nèi)廢鋼進(jìn)行連續(xù)預(yù)熱,入爐前廢鋼預(yù)熱溫度為200~400 ℃;預(yù)熱后的廢氣經(jīng)燃燒室進(jìn)入預(yù)熱回收系統(tǒng)。Consteel電弧爐實(shí)現(xiàn)了廢鋼連續(xù)預(yù)熱、連續(xù)加料、連續(xù)熔化、平熔池冶煉,提升了生產(chǎn)率,改善了車間內(nèi)外的環(huán)保條件,降低了電耗及電極消耗等。
早期豎式電弧爐在冶煉的同時,用天車料籃在豎井中加入下一爐所需廢鋼,用指形托架托住廢鋼,高溫廢氣直接與廢鋼接觸預(yù)熱,廢鋼溫度高達(dá)600~700 ℃。SHARC電弧爐(圖6)屬于改進(jìn)型豎爐式電弧爐,其*大的特點(diǎn)是電弧爐上有2個半圓形豎井,能保持豎井內(nèi)高溫廢氣對廢鋼進(jìn)行自然對流預(yù)熱,熔池平穩(wěn),其加料方式仍采用天車料籃;ECOARCTM生態(tài)電弧爐(圖4)利用豎爐豎井預(yù)熱廢鋼,可實(shí)現(xiàn)輕薄型廢鋼的連續(xù)加料,預(yù)熱溫度超過600 ℃,熔池穩(wěn)定,生產(chǎn)率高;Quantum電弧爐(圖7)屬于改進(jìn)型指形托架豎爐式電弧爐,通過爐頂廢鋼提升機(jī)提升傾動料槽將廢鋼分批加入豎井內(nèi),固定安裝豎井和爐蓋解決了原指形托架故障多的缺點(diǎn),傾翻爐體實(shí)現(xiàn)無渣出鋼。
環(huán)保型爐料預(yù)熱和連續(xù)加料系統(tǒng)EPC(environmental pre-heating and continuous charging system)是豎井型爐料預(yù)熱裝置,與其匹配的電弧爐采取較大的留鋼操作工藝(出鋼量的40%以上),因此此類電弧爐能平穩(wěn)地連續(xù)運(yùn)行。爐料通過側(cè)墻加料口連續(xù)地加到爐中,無需打開爐蓋,避免了熱量損失和煙氣排放。EPC系統(tǒng)可移動到電弧爐的上爐殼附近,與電弧爐側(cè)墻加料口及排煙道之間實(shí)現(xiàn)緊密銜接。其具體工藝流程如圖8所示。
各典型電弧爐技術(shù)指標(biāo)及廢鋼預(yù)熱*的對比見表8。通過總結(jié)電弧爐*預(yù)熱特征,可知廢鋼預(yù)熱技術(shù)未來發(fā)展趨勢:(1)電弧爐冶煉過程中全程密封,避免開蓋造成熱損失;水平加料式電弧爐雖預(yù)熱*有待進(jìn)一步提升,但其加料可控可靠,設(shè)備穩(wěn)定好;豎式電弧爐廢鋼預(yù)熱效率高,近年來新型電弧爐多為豎式加料結(jié)構(gòu);(2)平衡各類能源輸入量,注重物理余熱與化學(xué)余熱輸入對提高廢鋼預(yù)熱效率的作用,進(jìn)而改進(jìn)能源利用率提高電弧爐產(chǎn)能;(3)廢鋼預(yù)熱技術(shù)設(shè)計(jì)理念應(yīng)符合*新環(huán)保標(biāo)準(zhǔn),減少能源消耗,減少溫室氣體排放;(4)新型電弧爐煉鋼需綜合考慮廢鋼預(yù)熱、連續(xù)加料、平熔池冶煉、余熱回收、廢氣處理等方面,保證電弧爐煉鋼*、綠色化生產(chǎn)。
3
電弧爐智能化控制技術(shù)
近年來,一系列智能化監(jiān)測技術(shù)和控制模型在電弧爐煉鋼過程中得到應(yīng)用,如智能配料、電極智能調(diào)控、智能化取樣測溫、泡沫渣智能化監(jiān)測與控制、爐氣在線分析、終點(diǎn)成分預(yù)報(bào)、冶煉過程成本優(yōu)化和電弧爐煉鋼過程整體智能控制等,監(jiān)測和控制技術(shù)的應(yīng)用大幅度提高了電弧爐煉鋼過程的智能化水平。
3.1電極智能調(diào)節(jié)控制技術(shù)
電極調(diào)節(jié)控制技術(shù)是電弧爐實(shí)現(xiàn)智能化供電關(guān)鍵技術(shù)之一,其控制*直接影響電弧爐的電能消耗、冶煉周期等重要經(jīng)濟(jì)性能指標(biāo)。近年來,國際上較為成熟的智能電弧爐電極調(diào)節(jié)控制技術(shù)主要有3種:美國的IAFTM和SmartArcTM、德國的SimeltRNEC系統(tǒng)。國際典型電弧爐電極調(diào)節(jié)控制系統(tǒng)的技術(shù)對比見表9。
目前,基于PLC和工業(yè)計(jì)算機(jī)硬件平臺研發(fā)的SIMETAL電極控制系統(tǒng)是*新的電弧爐智能化電極控制系統(tǒng),圖9所示為SIMETAL Simelt系統(tǒng),該控制系統(tǒng)能根據(jù)實(shí)際工藝需求作出動態(tài)響應(yīng),提高工藝效率。在此基礎(chǔ)上,下一代電極控制系統(tǒng)的研發(fā)主要集中在過程參數(shù)及算法自適應(yīng),數(shù)據(jù)記錄、數(shù)據(jù)評估及集成過程可視化,可靠性高等方面。
3.2電弧爐智能化取樣測溫
電弧爐煉鋼過程中鋼液溫度測量和取樣所消耗的時間等是制約電弧爐電能消耗和生產(chǎn)效率的關(guān)鍵環(huán)節(jié)之一。針對傳統(tǒng)人工測溫取樣安全性差、成本高等問題,開發(fā)并推廣應(yīng)用一系列自動化測溫取樣新技術(shù)。目前較先進(jìn)的測溫方式是機(jī)器人全自動測溫和非接觸式測溫。
奧鋼聯(lián)推出的SIMETAL LiquiROB電弧爐機(jī)器人(圖10)能執(zhí)行全自動測溫和取樣操作,能自動更換取樣器和測溫探頭以及檢測無效測溫探頭等,同時還能通過人機(jī)界面實(shí)現(xiàn)全自動控制。
SIMETAL RCB Temp(圖11)是奧鋼聯(lián)開發(fā)的一種非接觸式溫度測量系統(tǒng),其依靠超音速氧氣射流技術(shù),在加料期間對廢鋼進(jìn)行預(yù)熱,加快廢鋼熔化速度,在精煉期以超音速射流噴吹氧氣,一旦達(dá)到規(guī)定的溫度均勻性水平,系統(tǒng)切換到溫度模式,以極短的時間間隔對溫度進(jìn)行分析。
3.3泡沫渣智能化監(jiān)測與控制
電弧爐的泡沫渣工藝主要通過目視觀察和人工噴碳操作相結(jié)合的方式進(jìn)行?;陔娏餍盘柡椭C波含量的半自動系統(tǒng)只能在一定程度上協(xié)助操作人員完成泡沫渣工藝過程。優(yōu)化泡沫渣智能化監(jiān)測與控制方案,確保電弧和熔池完全被泡沫渣穩(wěn)定地覆蓋,既能節(jié)約資源和降低電耗,也有利于降低生產(chǎn)成本和減少熱損失,是冶煉工藝實(shí)現(xiàn)全自動運(yùn)行的重要方面。
Siemens開發(fā)的Simelt SonArc FSM 泡沫渣監(jiān)控系統(tǒng)(圖12)保證了泡沫渣工藝的全自動進(jìn)行,聲音傳感器為精確監(jiān)測和分析泡沫渣高度奠定了基礎(chǔ);同時,泡沫渣高度的監(jiān)測為自動噴碳操作提供指導(dǎo),從而*大限度降低消耗指標(biāo)。
美國PTI 公司開發(fā)的電弧爐爐門清掃和泡沫渣控制系統(tǒng)PTI SwingDoorTM(圖13)能減少外界空氣的進(jìn)入,提高煉鋼過程的密封性;其集成氧槍系統(tǒng)代替了爐門清掃機(jī)械手或爐門氧槍自動清掃爐門區(qū)域。該系統(tǒng)通過控制爐門開合控制流渣,實(shí)現(xiàn)控制爐內(nèi)泡沫渣存在時間,進(jìn)而保證冶煉過程中爐膛內(nèi)渣層的厚度,減少能源消耗,提高電弧傳熱效率。
3.4電弧爐煉鋼過程整體智能控制
電弧爐智能化控制并非局限于某一設(shè)備的自動化、某一環(huán)節(jié)監(jiān)測與控制的智能化,而是從整體電弧爐煉鋼出發(fā),從*初配料到*終出鋼整個冶煉過程的數(shù)據(jù)采集與過程機(jī)理和工藝操作相結(jié)合,進(jìn)行數(shù)據(jù)分析、數(shù)據(jù)決策、數(shù)據(jù)評估以及*后流程控制,實(shí)現(xiàn)電弧爐煉鋼過程整體優(yōu)化,減少人為干預(yù),以此達(dá)到電弧爐煉鋼過程整體智能控制。
達(dá)涅利Q-Melt自動電弧爐系統(tǒng)(圖14)集成了過程控制監(jiān)視器和管理器,可自動識別電弧爐煉鋼過程預(yù)期行為的偏差,并使其自動返回到預(yù)定的冶煉過程。此系統(tǒng)主要包括Q-REG Plus電極動態(tài)調(diào)節(jié)控制系統(tǒng)、LINDARC廢氣分析系統(tǒng)和MELT-MODEL過程控制和優(yōu)化系統(tǒng)。其中MELT-MODEL過程控制和優(yōu)化系統(tǒng)是Q-MELT系統(tǒng)核心,與電極調(diào)節(jié)系統(tǒng)和廢氣分析系統(tǒng)相配合,通過化學(xué)成分分析或電氣特性曲線進(jìn)行動態(tài)調(diào)整電弧爐冶煉工藝,使冶煉過程始終保持*佳工藝狀態(tài)。
Tenova開發(fā)的iEAF智能控制系統(tǒng)(圖15)依靠傳感器反饋的工藝信息(如廢氣分析、電諧波、電流和電壓)和可控參數(shù)(氧氣和燃料流量、氧氣噴吹、*噴吹和電極管理)對電弧爐進(jìn)行*控制。此系統(tǒng)通過減少冶煉操作變數(shù),增強(qiáng)電弧爐運(yùn)行穩(wěn)定性從而提高生產(chǎn)效率、改善生產(chǎn)管理、節(jié)能降耗和減少CO2排放。
4
結(jié)論與展望
電弧爐煉鋼在“節(jié)能降耗、提高生產(chǎn)率”思想指導(dǎo)下,開發(fā)了諸多*化冶煉、綠色化生產(chǎn)和智能化控制方面技術(shù),并且綠色化和智能化技術(shù)在電弧爐煉鋼未來發(fā)展中的重要性將日益突出。未來電弧爐煉鋼將進(jìn)一步優(yōu)化基于配料、供電、供氧、輔助能源輸入、造渣等全流程電弧爐智能化監(jiān)測及控制模型和整體智能控制模型,開發(fā)低能源消耗、少污染物排放以及資源循環(huán)利用的綠色化生產(chǎn)技術(shù),完善集操作、工藝、質(zhì)量、成本、環(huán)保等于一體的電弧爐煉鋼流程,*終實(shí)現(xiàn)電弧爐綠色、智能、*和低成本煉鋼的目標(biāo),進(jìn)一步推動鋼鐵工業(yè)轉(zhuǎn)型升級。
5
參考文獻(xiàn)
略。
6
引用本文
姜周華, 姚聰林, 朱紅春, 潘濤. 電弧爐煉鋼技術(shù)的發(fā)展趨勢[J]. 鋼鐵, 2020, 55(7): 1-12. JIANG Zhou-hua, YAO Cong-lin, ZHU Hong-chun, PAN Tao. Technology development trend in electric arc furnace steelmaking[J]. Iron and Steel, 2020, 55(7): 1-12.
7
免費(fèi)下載全文鏈接
https://p3.itc.cn/q_70/images03/20230823/1b8cf86a69be4c31b5f8ecdddc1bd097.png8"font-size: 16px;"> 來源:《鋼鐵》2020年第7期
END
版權(quán)所有:山西北都科技股份有限公司 備案號:晉ICP備2022006699號-1